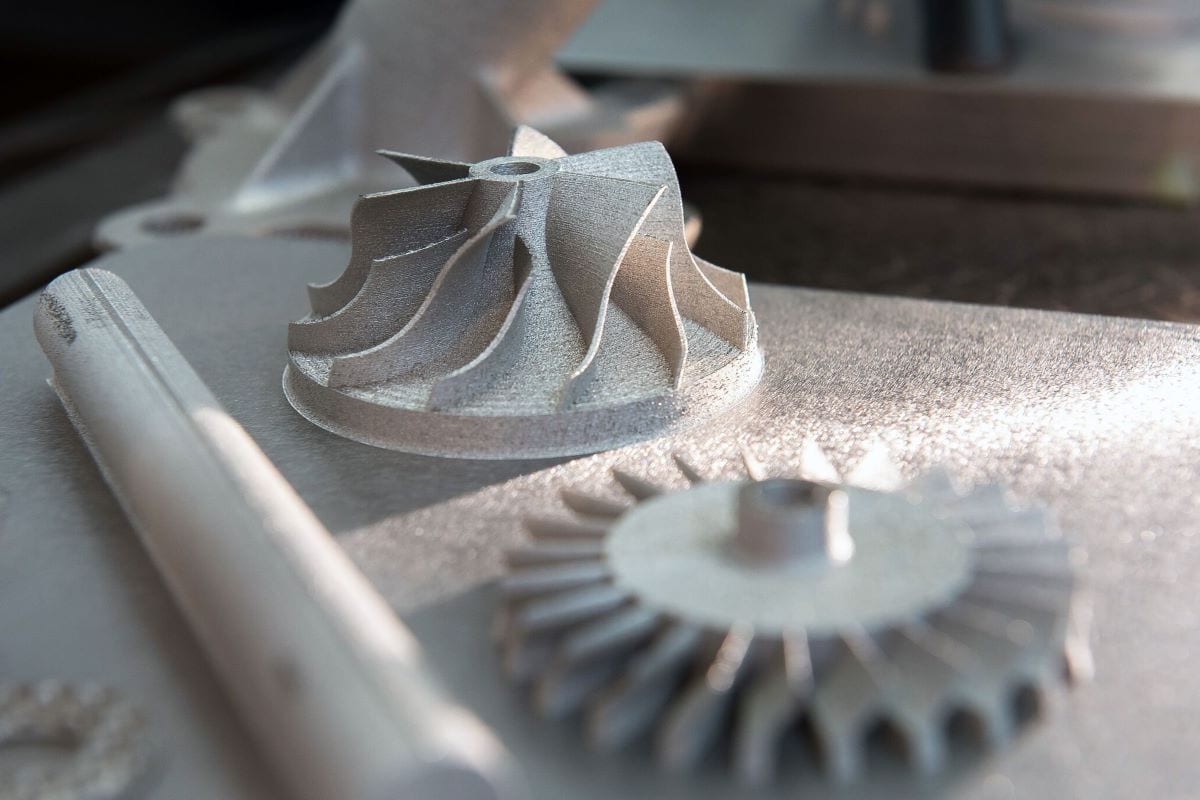
Table of Contents
Introduction
The realm of 3D printing has always held a certain mystique. From the early days when it conjured images of intricate plastic designs popping to life in labs, it has unfailingly captured the imagination of tech aficionados and laypersons alike. But as we stand at the precipice of an era marked by rapid technological advancements, the question arises: can 3D printers print metal?
At first, the very idea might seem plucked straight out of a science fiction novel. Visualizing a printer crafting detailed, sturdy, and usable metal objects might seem far-fetched, especially for those who’ve known 3D printing primarily for its polymer outputs. But as we’ll see, this isn’t just a flight of fancy. The science and art of 3D printing have progressed leaps and bounds, forging (quite literally) into territories previously thought impossible.
Through the course of this article, we will embark on a journey, retracing the steps of innovators and pioneers who dared to dream beyond plastic filaments. We will dive deep into the mechanisms, methods, and marvels of metal 3D printing. By the end, we hope to not only answer the burning question but also shed light on why and how metal 3D printing is poised to revolutionize industries.
But before we delve into the specifics, it’s essential to understand the rich tapestry of events, discoveries, and inventions that paved the way for this innovation. So, join us as we travel back in time, exploring the history and evolution of metal 3D printing.
History and Evolution of Metal 3D Printing
The story of metal 3D printing is an intricate blend of vision, serendipity, and technological evolution. To truly grasp the magnitude of its significance, one must peer into the annals of history, back to a time when 3D printing was still in its nascent stage, restricted to plastic materials and simple designs.
Early Metal Printing Methods
Though most might assume that metal 3D printing is a recent phenomenon, its roots trace back to the 1980s. Engineers and scientists had already begun toying with the idea of creating metal parts layer by layer, much before it became a household concept. Early experiments in this domain utilized methods like stereolithography, the brainchild of Dr. Chuck Hull, which utilized UV lasers and photosensitive resin. While not directly creating metal parts, these foundational technologies paved the way for what was to come.
Transition to Commercial Applications
As the 1990s rolled around, the potential of additive manufacturing became increasingly evident. Businesses across various industries recognized the value of producing complex metal parts without the need for extensive tooling or waste. The aviation and automotive sectors, always on the lookout for lighter yet robust parts, were among the first to explore commercial applications. Companies like GE Aviation began to harness 3D metal printing for producing specific components, such as fuel nozzles, that were not just lighter but also more efficient than their traditionally manufactured counterparts.
It wasn’t just large corporations that recognized this potential. Entrepreneurs and startups dabbled in creating affordable 3D metal printers for broader market accessibility. One notable name from this era is ExOne, which introduced Binder Jetting, a method we’ll explore further in the next section. Their vision was clear – to make metal 3D printing accessible not just for large industries but also for small businesses and innovators.
The New Millennium and Beyond
With the advent of the 21st century, the possibilities seemed endless. Advancements in technology, software, and materials science combined to propel metal 3D printing into the mainstream. Research institutions and universities, backed by governmental and private funding, delved deeper into refining techniques, materials, and applications. This period witnessed the rise of companies like EOS and SLM Solutions, pioneers in Laser Powder Bed Fusion – a technique that would soon become synonymous with high-precision metal 3D printing.
As we moved further into the 2000s, it wasn’t just about creating parts; it was about revolutionizing entire industries. Medical, aerospace, defense, jewelry – the list of sectors transformed by metal 3D printing continued to grow. Custom implants, lightweight satellite parts, intricate jewelry designs, all became achievable, thanks to the relentless advancements in metal additive manufacturing.
Today, as we stand at the cusp of another technological renaissance, metal 3D printing isn’t a question of possibility but of potential. With its history as a testament to human ingenuity and vision, one can only wonder: what methods and techniques lie in the horizon? Let’s delve deeper into the intricate methods of metal 3D printing in our next section.
Methods of Metal 3D Printing
Metal 3D printing, much like the metal it molds, isn’t a monolithic entity but a spectrum of varied techniques and processes, each with its unique advantages and applications. As the technology matured, so did the methods, branching out to cater to specific industry needs. Let’s journey through the primary techniques that have reshaped the landscape of metal manufacturing.
Direct Metal Laser Sintering (DMLS)
One of the most prevalent methods in metal 3D printing is Direct Metal Laser Sintering (DMLS). Rooted in the principle of sintering, it uses a high-powered laser to fuse metal powder particles together, layer by layer. The result? High-precision components ideal for sectors demanding meticulous detail, like the aerospace and medical fields. Companies such as EOS have been at the forefront, offering DMLS machines that cater to various industrial needs.
Electron Beam Melting (EBM)
While lasers are brilliant, they aren’t the only game in town. Enter Electron Beam Melting (EBM). As the name suggests, this method deploys a potent electron beam, controlled by magnetic fields, to melt and fuse metal powders. Renowned for its ability to manufacture dense and durable parts, EBM has become a staple in the medical and aerospace industries. Arcam, now a part of GE Additive, spearheaded this technology, giving manufacturers a robust alternative to traditional methods.
Binder Jetting
Shifting gears from lasers and beams, Binder Jetting brings a fresh approach to the table. Instead of directly melting metal powders, this method first binds them using a liquid adhesive. The subsequent ‘green part’ then undergoes post-processing where it’s sintered in a furnace to achieve full density. One of the hallmarks of this method is its ability to produce parts at a larger scale and at a quicker pace. Pioneering this technique, companies like ExOne and HP offer printers that cater to industries ranging from automotive to architecture.
Directed Energy Deposition (DED)
If we’re talking versatility, Directed Energy Deposition (DED) certainly earns its spot in the limelight. DED machines use a multi-axis arm to deposit metal powder or wire, which is instantaneously melted using a laser or electron beam. This on-the-go melting allows for additive and subtractive manufacturing in a single setup. Its prowess shines particularly in repair and maintenance jobs, where worn-out parts can be restored without a complete overhaul. Leaders in this domain include Optomec with its LENS series, championing DED’s capabilities for diverse applications.
In addition to these primary methods, several niche techniques cater to specific needs, from creating porous structures ideal for bone integration in medical implants to manufacturing intricate jewelry designs that defy traditional craftsmanship.
Each of these methods, with their unique strengths, has played a pivotal role in pushing the boundaries of what’s possible with metal 3D printing. But like any technology, metal 3D printing isn’t just about the methods and machines; it’s about the impact, the transformation it brings to industries, and the value it adds to products and processes. Let’s delve into the myriad advantages of this groundbreaking technology in our next section.
Advantages of Metal 3D Printing
Unshackling creators from the constraints of traditional manufacturing, metal 3D printing heralds a new era of limitless possibilities. It’s not just about conjuring objects from a pool of molten metal; it’s about redefining the boundaries of design, innovation, and efficiency. As industries across the globe embrace this technological marvel, let’s explore the compelling advantages that make metal 3D printing the crown jewel of modern manufacturing.
Design Freedom
Imagine a world where your design aspirations aren’t tethered to the limitations of conventional tools. Metal 3D printing grants designers this very liberty, allowing them to breathe life into intricate geometries and complex structures that would be challenging, if not impossible, with traditional methods. This freedom fosters innovation, enabling industries to craft bespoke components tailored to specific needs, from lightweight aircraft parts to patient-specific medical implants.
Reduced Waste
Traditional manufacturing often resembles sculpture, carving out objects from larger blocks of material. This subtractive process, while effective, generates significant waste. Enter metal 3D printing. By building objects layer by layer, only the necessary amount of material is used, dramatically reducing waste and making the process more sustainable and cost-effective. Companies like Markforged emphasize this benefit, championing efficient material usage in their printing processes.
Speedy Prototyping
Time, they say, is money. And in the fast-paced world of product development, the ability to quickly transition from design to prototype is invaluable. Metal 3D printing accelerates this journey, enabling engineers to promptly test and refine designs without the prolonged lead times of mold creation or tooling adjustments. This rapid prototyping capability not only hastens time-to-market but also fosters a culture of iterative improvement, propelling product quality to new heights.
On-Demand Production
In an era where customization is king, the ability to produce on-demand, without the need for vast inventories, is a game-changer. Metal 3D printing facilitates this shift, allowing manufacturers to produce parts as and when needed, minimizing storage costs and reducing the carbon footprint associated with large-scale production and shipping. Desktop Metal, with its suite of printers, is pioneering this movement, offering solutions that cater to both large industries and smaller enterprises.
Consolidation of Parts
Why assemble from many when you can craft from one? Metal 3D printing offers the unique advantage of creating single, integrated parts that would otherwise require assembly from multiple components. This consolidation not only enhances the strength and integrity of the final product but also trims down production costs and timelines associated with assembly processes.
Enhanced Material Properties
It’s not just about shape and structure; it’s also about substance. Metal 3D printing can result in parts with enhanced material properties, often exhibiting superior strength, durability, and resistance compared to their traditionally manufactured counterparts. Techniques like DMLS and EBM ensure a high degree of control over the microstructure of the final product, often resulting in better performance metrics.
In conclusion, the advantages of metal 3D printing stretch far beyond mere novelty. It’s a transformative force, reshaping industries, catalyzing innovation, and setting new benchmarks for efficiency, sustainability, and excellence. But like all technologies, it’s not without its challenges. Dive with us into the next section as we unravel the complexities and limitations of metal 3D printing.
Challenges and Limitations
Like a double-edged sword, metal 3D printing’s undeniable allure comes accompanied by a suite of challenges that sometimes temper the enthusiasm surrounding it. While the advantages paint a picture of limitless potential, it’s essential to also understand the hurdles and limitations standing in the way of its universal adoption. So, buckle up as we navigate through the intricate labyrinth of challenges that the world of metal 3D printing presents.
Technical Complexity
From ensuring the right thermal environment to maintaining a precise laser focus, the technical nuances of metal 3D printing are manifold. Any minor aberration can lead to defects, porosity, or warping in the final product. Companies such as EOS and GE Additive invest heavily in research to mitigate these issues, but achieving consistent results across varied applications remains a challenge.
Post-Processing Needs
The journey doesn’t end once an item emerges from the printer. Metal 3D printed parts often require extensive post-processing, such as heat treatments, machining, or surface finishing, to meet desired specifications. This not only adds to production time but also escalates costs, sometimes offsetting the initial advantages of rapid production.
Material Limitations
Contrary to popular belief, not all metals are fit for 3D printing. While the repertoire of printable alloys is expanding, certain metals and alloys pose challenges due to their melting properties, thermal behavior, or inherent characteristics. This restricts designers and industries from leveraging the full spectrum of metal materials available conventionally.
High Initial Costs
The dream of creating metal wonders layer-by-layer comes at a price. High-quality metal 3D printers and the associated infrastructure often demand substantial initial investments. Though the cost is steadily declining with technological advancements and market maturity, it still presents a significant barrier for small to medium-sized businesses to adopt metal 3D printing readily.
Knowledge and Skill Gap
Operating a metal 3D printer isn’t as straightforward as using its plastic counterpart. It demands a deep understanding of metallurgy, design considerations, and machine operation specifics. The industry grapples with a skill and knowledge gap, with trained professionals in metal 3D printing still in limited supply. Institutions and companies are ramping up training programs, but bridging this gap will take time.
Size Constraints
Size does matter in the realm of metal 3D printing. While creating intricate and miniature parts is a breeze, scaling up to larger components poses challenges. Printers with large build volumes are not just expensive but also grapple with issues like maintaining uniform temperature throughout the print, leading to potential inconsistencies in the final product.
In essence, while metal 3D printing stands as a beacon of modern manufacturing, its challenges remind us of the continuous evolution required in the space. As with any emerging technology, there are teething issues. But given the pace of technological advancements and the relentless human spirit, the future looks promising, with many of these challenges set to be mere footnotes in the annals of history. Speaking of the future, let’s cast our gaze forward and envisage what lies ahead for metal 3D printing.
The Future of Metal 3D Printing
Peering into the horizon of metal 3D printing is like stepping into the pages of a science fiction novel. From constructing lunar bases to creating bespoke jewelry, the promises are both monumental and intimately personal. Let’s voyage together into the not-so-distant future and uncover the fascinating prospects metal 3D printing has in store for us.
Expanded Material Palette
The future promises an even broader spectrum of metals and alloys tailored for 3D printing. Companies like Materialise and Desktop Metal are already pushing boundaries, researching novel materials that can deliver unique properties, marrying the best of strength, flexibility, and finish.
Integration with AI and Machine Learning
Imagine a 3D printer that learns from every layer it prints, optimizing itself in real-time. With the integration of artificial intelligence and machine learning, this isn’t just a pipe dream. Such advancements will drastically reduce errors, enhance printing speed, and ensure superior product quality consistently.
More Sustainable Production
As our global consciousness tilts towards sustainability, metal 3D printing is poised to play a pivotal role. With its potential to reduce waste significantly and its ability to leverage recycled materials, the eco-credentials of metal 3D printing will shine even brighter in the years to come.
Larger Print Sizes
The constraints of today will not bind the giants of tomorrow. Companies like Relativity Space are already dabbling in massive 3D printed rocket components. The day isn’t far when constructing larger components, perhaps even entire vehicles or building structures, could be achieved seamlessly.
Localized Manufacturing
One of the most transformative impacts of metal 3D printing lies in its potential to democratize manufacturing. With the flexibility it offers, industries won’t be tethered to massive centralized factories. Instead, local manufacturing hubs could cater to specific community needs, reshaping global supply chains and bolstering local economies.
Biomedical Breakthroughs
The fusion of medicine and metal 3D printing is still in its nascent stages, but the potential is staggering. Custom implants, bone replacements, or even organ scaffolds could be crafted to an individual’s unique anatomy. Brands like Medtronic and Johnson & Johnson are heavily invested in this space, heralding a new era of personalized medicine.
In the vast expanse of the future, metal 3D printing stands as a beacon of innovation, ready to redefine industries and touch lives in ways we’re only beginning to fathom. But as we dream of tomorrow, let’s not forget to ground ourselves in the present and reflect on the journey of this transformative technology.
Conclusion
As we wrap up our journey through the riveting world of metal 3D printing, it’s evident that this technology isn’t merely about building structures layer by layer; it’s about reshaping industries, reimagining possibilities, and rewriting the rules of manufacturing. From its humble origins to its futuristic prospects, metal 3D printing stands as a testament to human ingenuity and the relentless pursuit of innovation.
The past has shown us how metal 3D printing evolved from a niche concept into a transformative force. Today, it powers everything from aerospace marvels to life-altering medical implants. And tomorrow? It promises to redefine how we think about manufacturing, ushering in an era of sustainability, personalization, and local production.
Yet, as with all technologies, it’s crucial to approach metal 3D printing with a balanced perspective. While the advantages are many, the challenges remind us that there’s still work to be done, research to be conducted, and limitations to be overcome.
So, whether you’re an entrepreneur seeking the next big thing, a designer aiming to bring visions to life, or a curious mind hungry for knowledge, metal 3D printing beckons with a world of opportunities. Let’s embrace it with open arms, celebrate its achievements, and eagerly anticipate its contributions to a brighter, more innovative future.
Thank you for joining us on this exploration. Here’s to the endless horizons and the limitless potential of metal 3D printing!